Have you ever thought about how your favorite items show up at your door right when you need them?
What if they were always late?
Supply Chain Management (SCM) is the behind-the-scenes magic that fixes this problem. It makes sure things arrive on time and don’t cost too much.
SCM connects all the steps to get products from start to finish, turning possible delays into smooth delivery.
🌟 Understanding Supply Chain Management: A Key to Business Success
In today’s globalized market, the efficiency and responsiveness of a business’s supply chain can be the difference between success and failure.
Supply Chain Management (SCM) is the critical backbone that ensures business operations are smooth, cost-effective, and customer-centric.

🤔 What is Supply Chain Management?
Supply Chain Management refers to the comprehensive coordination of a business’s supply-side activities to maximize customer value and gain a competitive advantage in the marketplace.
It involves the active management of supply chain activities to optimize the flow of goods, data, and finances from supplier to consumer. SCM integrates supply and demand management within and across companies.
⏩ The Goals of Supply Chain Management
The primary goal of SCM is to ensure that products are available at the right locations and at the right time without compromising quality and cost. The objectives can be distilled into five key areas:
- Cost Reduction – Streamlining operations to reduce costs associated with manufacturing and distribution.
- Increased Efficiency – Enhancing the speed of product delivery by optimizing various supply chain processes.
- Demand Management – Balancing customer demands with supply capacities.
- Mitigation of Risks and Disruptions – Identifying and managing potential risks in the supply chain to avoid delays and disruptions.
- Innovation and Sustainability – Developing new strategies to meet environmental standards and achieve long-term sustainability goals.
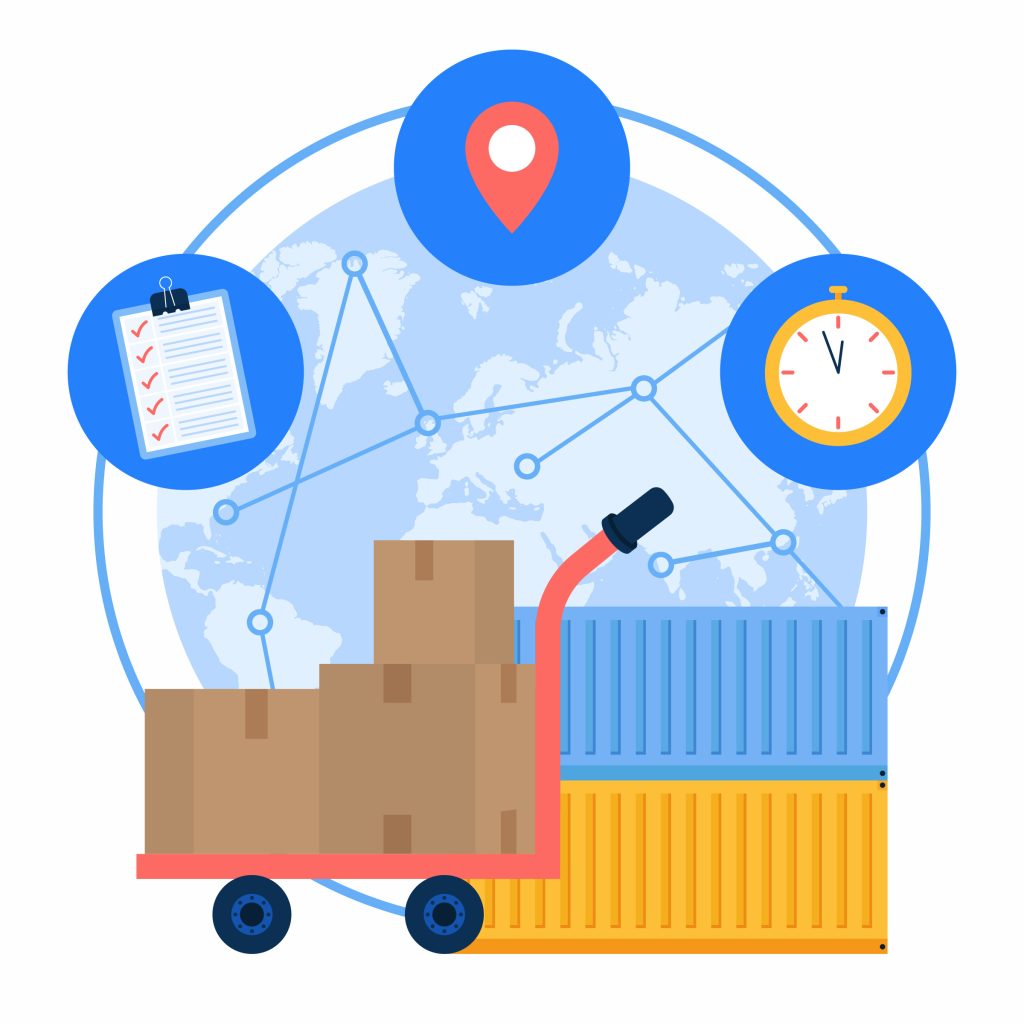
✨ How Does Supply Chain Management Work? A Step-by-Step Guide
1. Planning and Strategy: Aligning Production with Demand
Planning and Strategy involves creating strategic plans to ensure that products meet consumer demands while remaining cost-effective.
This stage is crucial for determining what products to sell, predicting customer demand, managing inventory levels, and deciding on production quantities—all while keeping an eye on costs.
2. Sourcing and Procurement: Finding the Right Suppliers
Sourcing and Procurement focuses on selecting suppliers who can provide the necessary goods and services to create the product.
This step is akin to sourcing the best ingredients for cooking; it’s about finding high-quality materials at reasonable prices and ensuring these materials are delivered on time to keep production running smoothly.
3. Manufacturing: Turning Raw Materials into Finished Goods
Manufacturing involves the activities required to transform raw materials into finished products. Effective manufacturing is essential for efficiently managing resources, including labor, machinery, and materials, to ensure that production processes are seamless and output meets established quality standards.
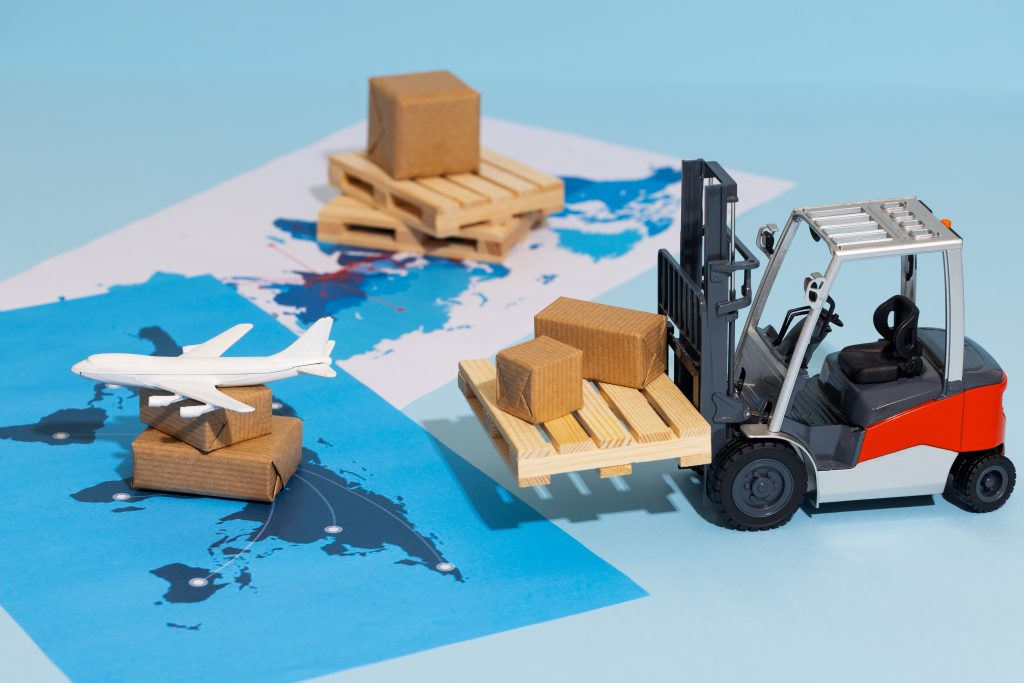
4. Delivery and Logistics: Efficient Product Distribution
Delivery and Logistics deals with the logistics of order fulfillment, including the transportation of goods from manufacturing facilities to consumers.
This component ensures that products are delivered efficiently, reaching customers in a timely manner and in perfect condition, which involves route planning, shipment tracking, and handling any logistical challenges that arise.
5. Returns Management: Handling Post-Purchase Issues
Returns Management is about efficiently managing the return of defective or unwanted products. This process includes assessing the returned items, deciding whether to repair, replace, or refund them, and handling the logistics of returns.
Effective returns management is key to maintaining customer satisfaction and minimizing waste and additional costs.
By focusing on these components, businesses can optimize their supply chain operations, ensuring customer satisfaction, reducing costs, and improving overall efficiency.
💫 Why is Supply Chain Management Important?
SCM is crucial because it directly affects a company’s efficiency and effectiveness in the market. Proper supply chain management can:
Here’s a simple explanation of how effective Supply Chain Management (SCM) can benefit a business in four key areas:
1. Reduce Operating Costs
By optimizing supply chain processes, companies can reduce their “cost of goods sold” (COGS), which includes the direct costs tied to the production of the goods a company sells (like material and labor costs).
Lowering these costs helps to improve profit margins—the difference between what it costs to produce the product and what it’s sold for. This means more money can stay in the company’s pocket, boosting its overall financial health.
2. Increase Output
SCM enhances the efficiency of production and supply processes, which leads to an increase in the amount of product a company can produce.
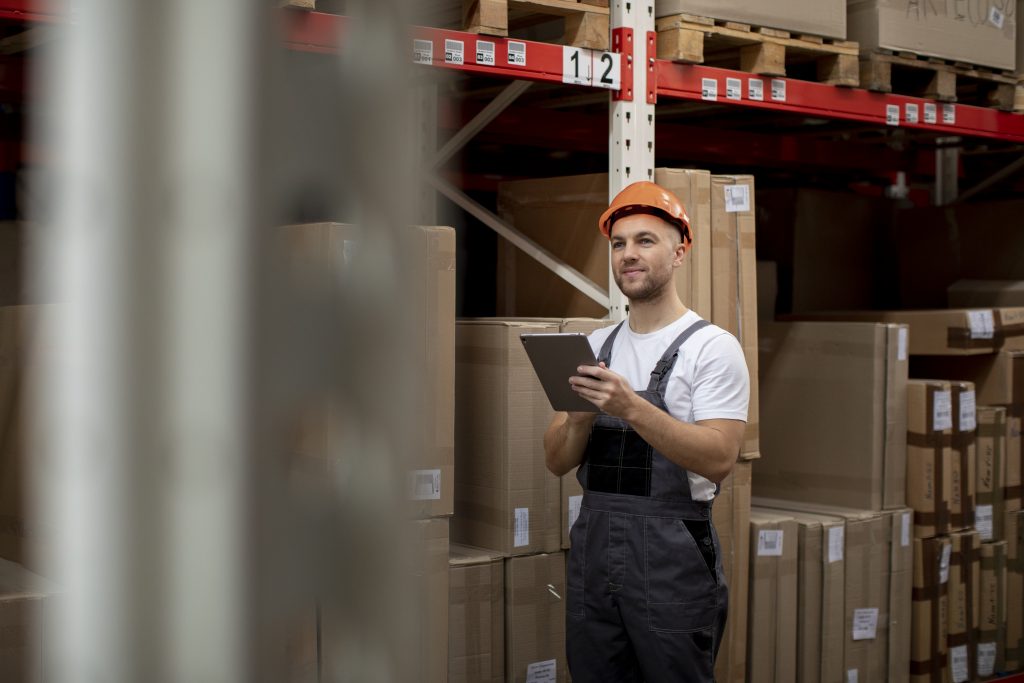
By improving relationships with suppliers and streamlining manufacturing processes, companies can produce more in less time. This not only helps meet customer demand more effectively but also opens opportunities for higher sales volumes.
3. Improve Customer Satisfaction
One of the key benefits of effective SCM is the ability to deliver products on time. When customers receive their products when expected, or even sooner, their satisfaction and trust in the company increase.
This reliability can lead to repeat business and customer loyalty, which are critical for long-term success. It also helps in building a positive brand reputation, as satisfied customers are more likely to recommend the company to others.
4. Enhance Risk Management
Supply chains are prone to various risks, including delays, disruptions, and sudden changes in demand or supply. SCM involves planning and strategizing to manage these risks effectively.
By having a solid risk management strategy, companies can quickly adapt to changes and disruptions, minimizing their impact on operations.
This includes having contingency plans in place, diversifying suppliers to avoid dependency on a single source, and continuously analyzing the supply chain for potential risks.
In sum, SCM plays a pivotal role in making a business more efficient, cost-effective, and resilient, all of which contribute to stronger, more competitive positioning in the market.
🔴 Challenges in Supply Chain Management
While SCM can provide numerous benefits, it also comes with its challenges:
Here’s a breakdown of the challenges faced in Supply Chain Management (SCM) due to globalization, technological changes, customer demand fluctuations, and regulatory and environmental concerns:
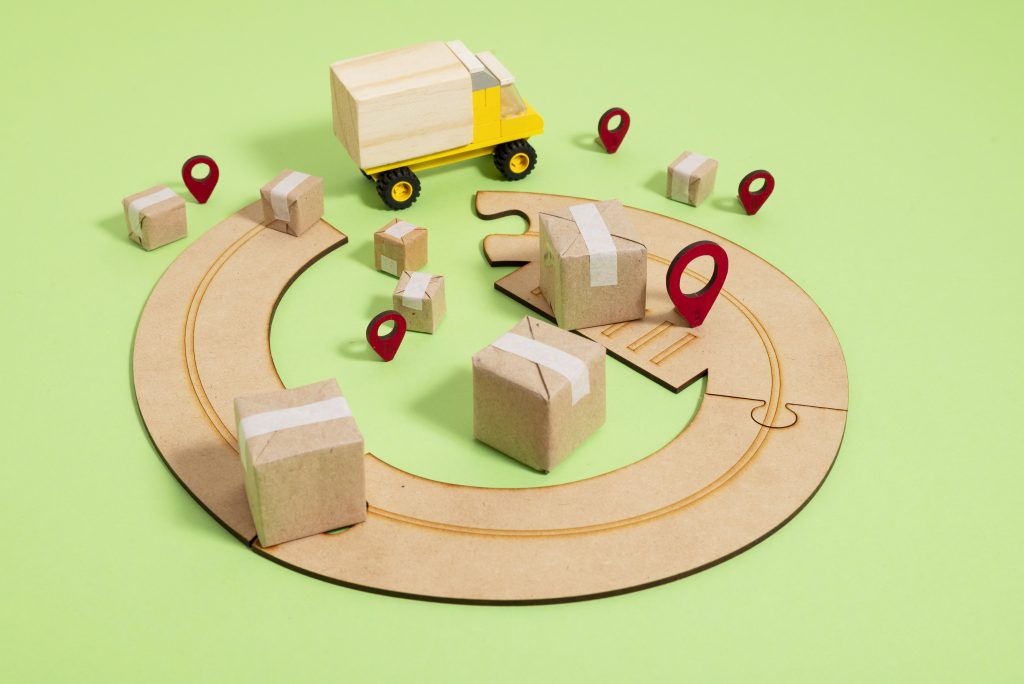
1. Globalization
Managing supply chains on a global scale introduces complexity and increases potential risks. Global supply chains involve coordinating with suppliers, manufacturers, and customers across different countries, each with its own regulations, cultural norms, and logistical challenges.
This complexity can lead to issues like longer lead times, increased costs of transportation, potential customs delays, and difficulties in quality control. Moreover, global supply chains are more vulnerable to disruptions from geopolitical tensions, economic instability, and global health crises.
2. Technological Changes
Technology is rapidly advancing, and keeping up can be challenging for businesses. In SCM, technologies such as automation, artificial intelligence, and blockchain are transforming how inventory is managed, how data is processed, and how transactions are recorded and verified.
While these technologies offer significant benefits, such as increased efficiency and better data accuracy, integrating them requires substantial investments in time and capital.
Additionally, there’s the challenge of training staff to use new systems and the risk of technological obsolescence.
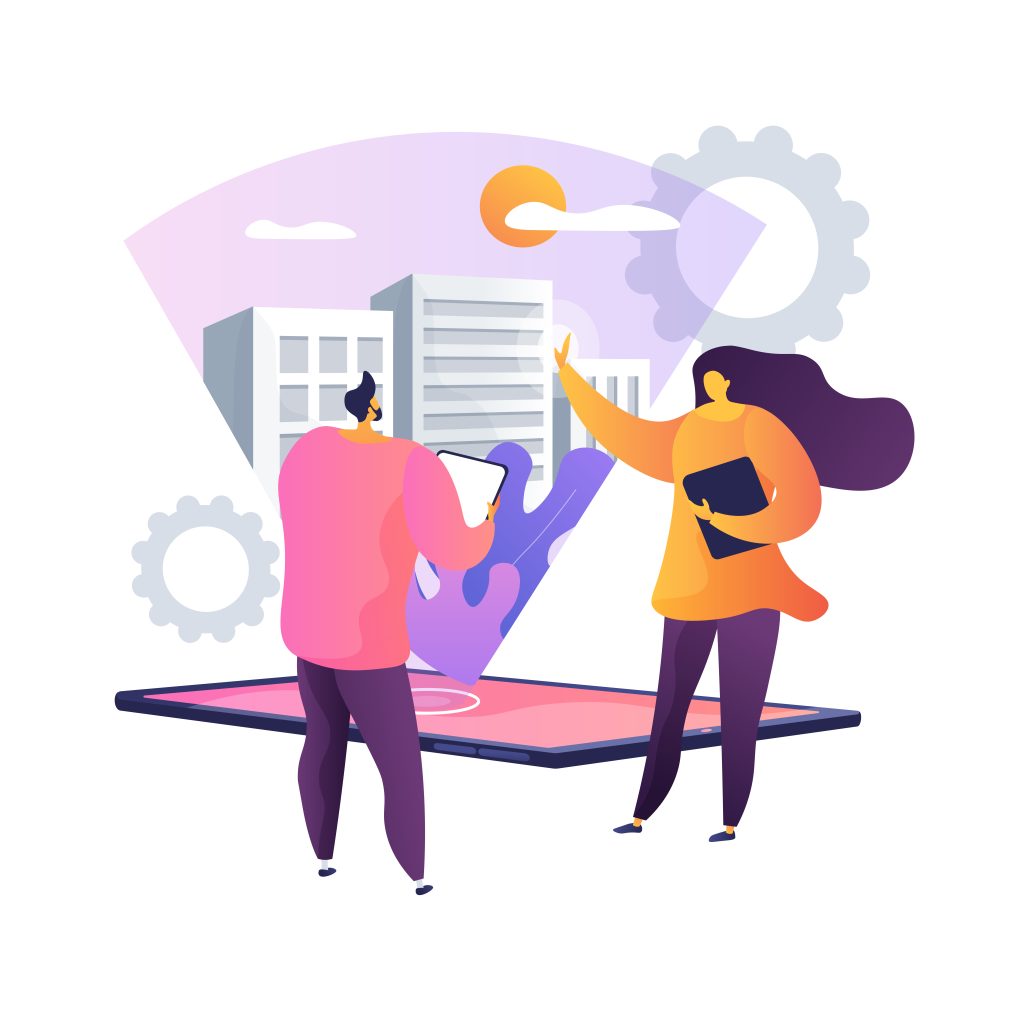
3. Customer Demand Fluctuations
Changes in customer demand can happen quickly and unpredictably, disrupting supply chains. For instance, a sudden increase in demand for a particular product can strain the supply chain if there isn’t enough inventory or production capacity.
Conversely, a drop in demand can lead to excess inventory and increased storage costs. Effective SCM must be agile, with robust demand forecasting and flexible inventory management strategies to respond swiftly to such fluctuations.
4. Regulatory and Environmental Issues
Supply chains must comply with a wide range of regulations that vary by country and region, including safety standards, labor laws, and customs regulations.
Moreover, there is growing pressure on companies to adopt sustainable practices. This includes reducing carbon footprints, minimizing waste, and using environmentally friendly materials.
Compliance requires ongoing vigilance and adaptation to new laws and societal expectations. While adhering to these regulations and practices can be costly and complex, they are crucial for legal compliance, maintaining brand reputation, and fulfilling corporate social responsibility.
Each of these challenges requires careful management and strategic planning to ensure that the supply chain remains resilient and capable of supporting the company’s business goals.
👉🏻 Which Supply Chain Model Fits Your Business Needs?
1. The Continuous Flow Model
This model is ideal for businesses that have a steady demand for their products, with little variation in the production process.
It’s often used by companies that manufacture the same products year-round without significant changes, such as basic household goods manufacturers.
The continuous flow model allows for a consistent production rate, minimizing disruptions and optimizing manufacturing efficiency.
2. The Fast Chain Model
Designed for industries where product life cycles are short and consumer trends change rapidly, such as fashion or technology, the fast chain model emphasizes speed and responsiveness.
It allows companies to quickly develop, manufacture, and deliver products to capitalize on current trends before they fade. This model requires a highly reactive supply chain setup with strong connections between design, production, and distribution.
3. The Efficient Chain Model
This model is used by companies focused on cost efficiency, typically for products in competitive markets where price is a key differentiator.
Retailers of generic household products or large-scale manufacturers of standard components often use this model.
It prioritizes high efficiency and volume, leveraging economies of scale to reduce costs, and often involves minimizing inventory levels and streamlining operations.
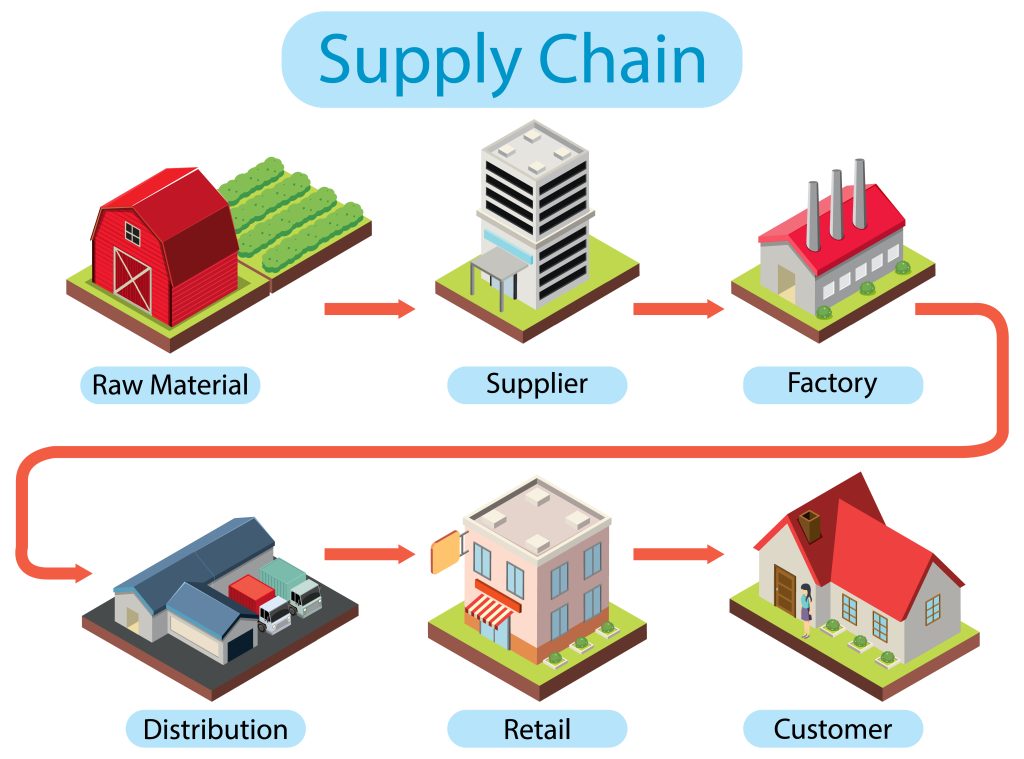
4. The Agile Model
Agility is crucial in environments where demand is both unpredictable and diverse. The agile model combines the elements of responsiveness and flexibility, enabling companies to adapt quickly to market changes and customer preferences.
This model is suitable for businesses that face significant demand fluctuations or that offer a wide variety of product configurations and customization options.
5. The Custom Configured Model
Certain products, such as computers or automotive, require assembly from standard components but are customized according to customer specifications.
The custom-configured model focuses on modular designs that can be assembled in various configurations to meet specific customer demands. This model balances the efficiency of mass production with the flexibility of customization.
6. The Flexible Model
The flexible model is designed for industries where production can be ramped up and down quickly. This is particularly useful for seasonal products or in industries like agriculture, where production levels can fluctuate significantly due to external factors such as weather.
Flexibility in capacity and inventory management is a hallmark of this model.
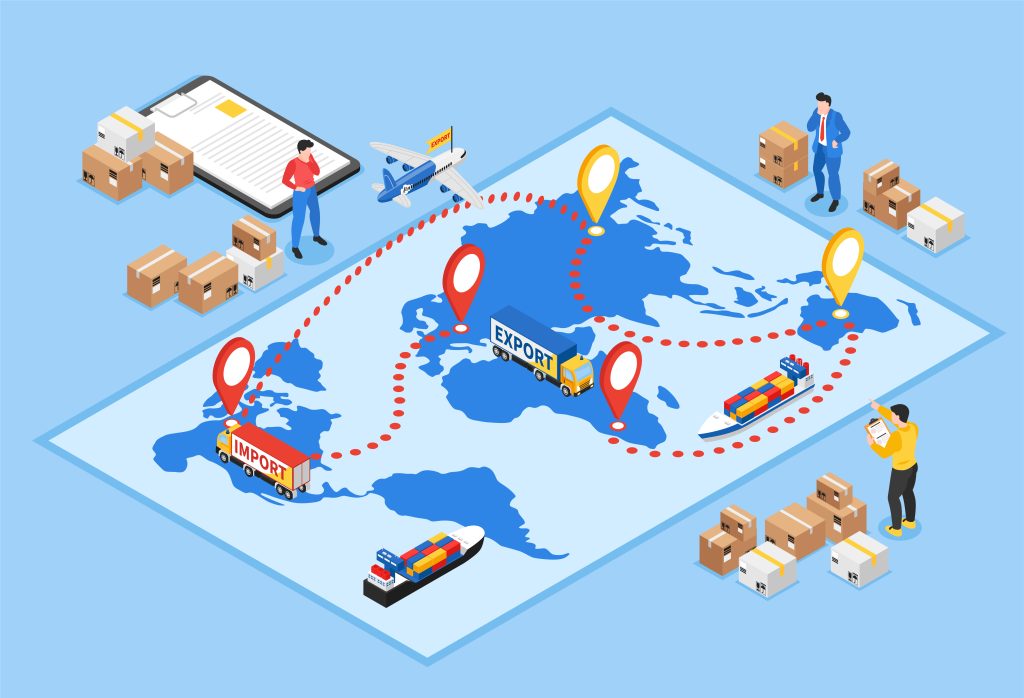
7. The Global Model
In the global model, companies operate in an integrated manner across multiple countries to leverage geographic benefits, such as low-cost labor or superior technology.
This model involves managing long lead times and dealing with complex logistics and often requires sophisticated coordination of production and distribution across diverse regulatory and cultural landscapes.
Each of these models addresses specific operational needs and market conditions. Choosing the right supply chain model involves understanding the unique aspects of a company’s products, market demands, and business strategy.
🚀 Case Study: How Shipchain Elevated TechGlobal Solutions’ Supply Chain Efficiency
Client Overview
TechGlobal Solutions, a prominent global supplier of consumer electronics, operates a sprawling supply chain with facilities in over 30 countries and partnerships with over 500 suppliers. Before using Shipchain, TechGlobal grappled with inefficient inventory management, unpredictable delivery schedules, and escalating operational costs, which hampered its market competitiveness and customer satisfaction.
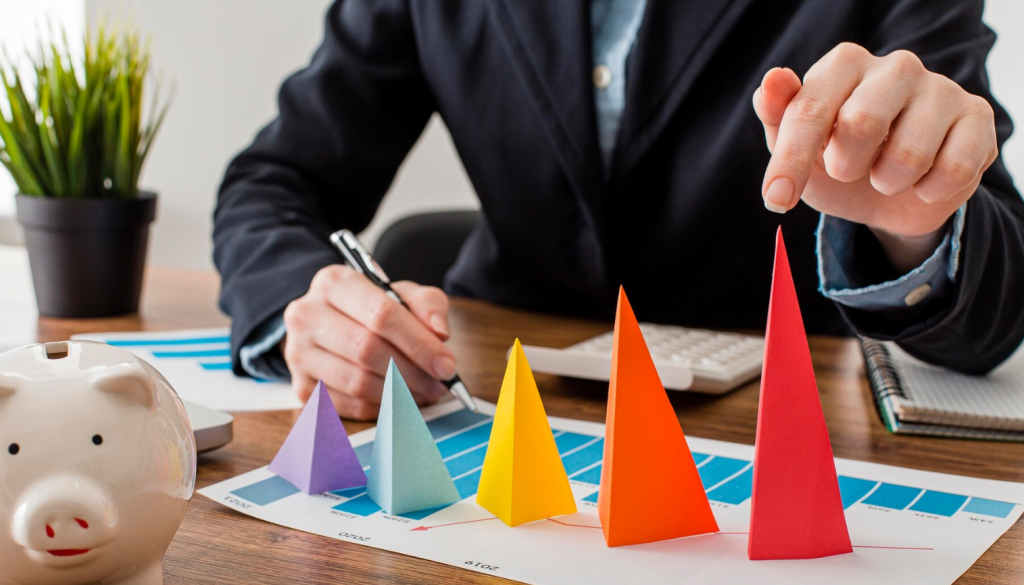
Challenges Faced
- Inefficient Tracking: TechGlobal could not monitor inventory and shipments accurately in real-time, leading to frequent occurrences of overstocking or stock shortages.
- Delayed Deliveries: Disconnected supply chain processes often result in product delivery delays, negatively affecting customer trust and retention.
- High Operational Costs: Operational inefficiencies, coupled with frequent delays, inflated the cost of operations, eroding profit margins by nearly 18%.
Implementation of Shipchain
In response to these challenges, TechGlobal Solutions adopted Shipchain, an advanced supply chain management software designed to enhance efficiency from procurement to delivery. Shipchain provided the following key solutions:
- Real-Time Tracking: Shipchain’s robust tracking system offered real-time visibility of inventory levels and shipment statuses, enhancing logistical accuracy.
- Automated Procurement: Leveraging predictive analytics, Shipchain’s automated procurement tools helped maintain optimal stock levels, reducing both overstock and stockout incidents by 40%.
- Optimized Logistics: The logistics optimization features in Shipchain improved route planning and scheduling, which cut down delivery times by 35% and transportation costs by 22%.
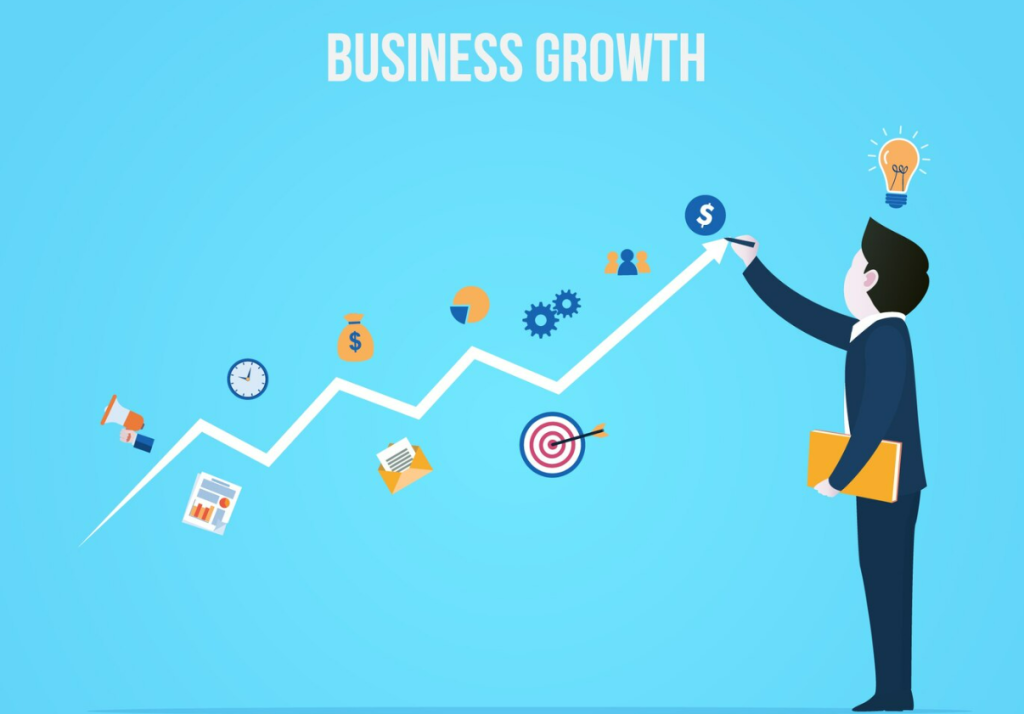
Results Achieved
- Reduced Operational Costs: Post-implementation, TechGlobal witnessed a 30% reduction in supply chain costs due to streamlined operations and minimized waste.
- Enhanced Delivery Efficiency: Improved scheduling and logistics cut down average delivery times from 14 days to 9 days, boosting customer satisfaction rates.
- Increased Visibility and Control: Enhanced tracking and management capabilities provided TechGlobal with greater control over its supply chain, facilitating better strategic decisions and quicker adaptability to market shifts.
Client Testimonial
“Implementing Shipchain was a game-changer for us. It not only reduced our costs but also enhanced our delivery performance, which has been critical in retaining our customers and improving their satisfaction. The detailed visibility into our supply chain operations has empowered us to make informed decisions swiftly,” remarked the COO of TechGlobal Solutions.
💸 Cost Analysis in Supply Chain Management
Cost analysis in Supply Chain Management (SCM) is a critical exercise that helps businesses understand the cost dynamics of their supply chain activities.
It involves evaluating all costs associated with sourcing, producing, and delivering products to consumers. The goal is to identify areas where costs can be reduced without compromising quality or customer satisfaction.
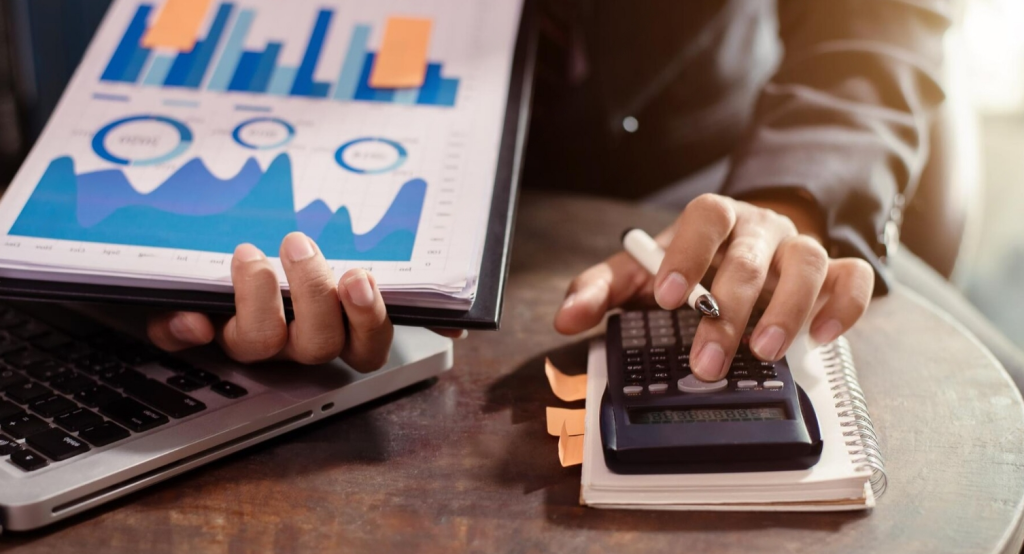
Here’s how cost analysis typically works in SCM:
1. Identification of Costs
The first step in cost analysis is to identify and categorize the different types of costs involved in the supply chain. These can include:
- Direct Costs: These are costs directly tied to the production of goods, such as raw materials, labor, and manufacturing expenses.
- Indirect Costs: These include overheads like salaries of management, utilities, and rent.
- Logistics Costs: Costs associated with storing and transporting goods, including warehousing, shipping, and handling fees.
- Procurement Costs: Expenses related to acquiring raw materials and goods, including supplier costs, purchasing operations, and transactions.
2. Quantifying Costs
After identifying the costs, the next step is to quantify them. This involves collecting data on each cost element, typically through accounting systems, invoices, and procurement records. This data needs to be accurate and reflective of current operations to provide a reliable basis for analysis.
3. Analyzing Costs
With detailed cost data in hand, businesses analyze these costs to see where money is being spent, how these costs align with other business operations, and where inefficiencies may lie. This analysis often involves looking at:
- Cost per unit: Understanding how much it costs to produce each unit of product.
- Cost-benefit analysis: Evaluating whether certain spending, like on faster shipping or better quality materials, actually leads to higher customer satisfaction or more sales.
- Benchmarking: Comparing costs against industry standards or competitors to identify areas for improvement.
4. Identifying Opportunities for Cost Reduction

The main objective of cost analysis is to find opportunities to reduce costs. This can involve:
- Negotiating better terms with suppliers to reduce procurement costs.
- Optimizing production processes to use less material or labor.
- Improving logistics to consolidate shipments, choose less expensive routes, or switch to more cost-effective carriers.
- Reducing waste through better inventory management or reducing excess packaging.
5. Implementing Changes
The final step is to implement the changes identified as opportunities for cost reduction. This might involve renegotiating contracts, purchasing new equipment, redesigning products, or changing suppliers. It’s crucial to monitor the impact of these changes to ensure they produce the desired cost-saving effects without lowering the quality of the product or service.
6. Continuous Monitoring and Improvement
Cost analysis is not a one-time activity but an ongoing process. Continuous monitoring of costs and performance allows companies to keep their operations cost-efficient and responsive to changes in the market or supply chain disruptions.
🤖 Future Trends in Supply Chain Management
Supply Chain Management (SCM) is continuously evolving, shaped by technological advancements, changing market dynamics, and global economic conditions. Here are some of the key future trends expected to influence SCM:
1. Increased Digitization and Automation
As technology advances, more supply chains will adopt digital solutions to enhance efficiency and accuracy. Automation, powered by robotics and artificial intelligence (AI), will play a crucial role in streamlining operations from inventory management to delivery.
For instance, autonomous vehicles and drones could revolutionize delivery methods, while AI could optimize inventory levels and predict maintenance needs.
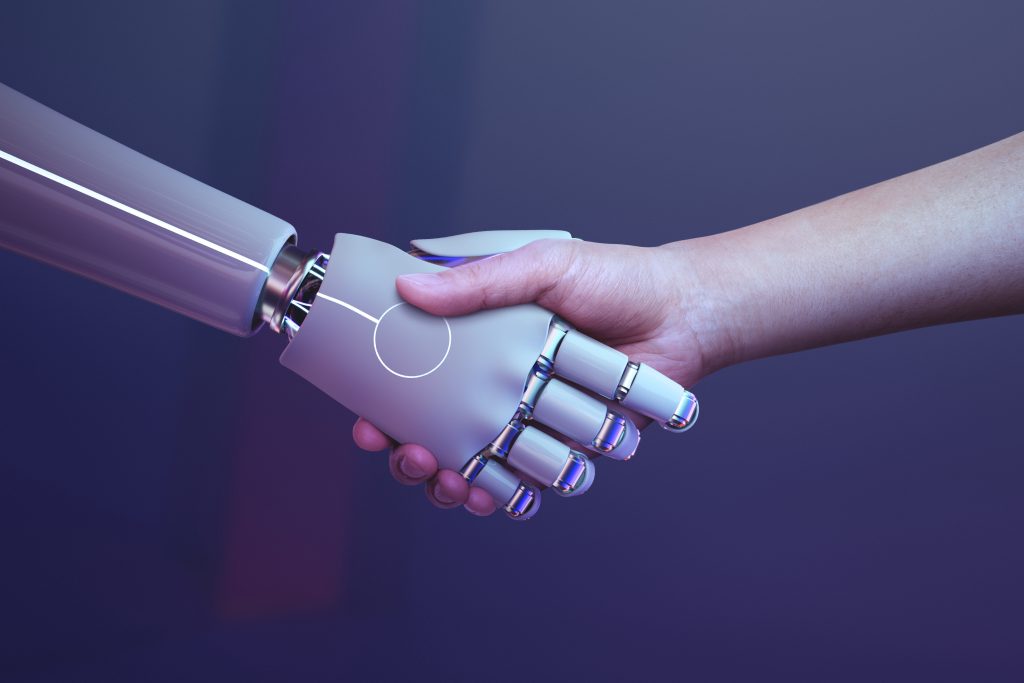
2. Integration of Blockchain Technology
Blockchain offers transparency and security in transactions, making it ideal for global supply chains. It can provide a tamper-proof record of every transaction, from raw material sourcing to final product delivery, ensuring traceability and reducing fraud.
This technology is particularly beneficial for industries requiring high compliance and traceability standards, such as pharmaceuticals and food and beverages.
3. Sustainability and Ethical Practices
Consumers are increasingly demanding sustainability and ethical practices from businesses. This trend is pushing companies to adopt green supply chain practices, such as reducing carbon footprints, optimizing resource usage, and ensuring fair labor practices.
Companies are exploring new packaging solutions, sustainable sourcing options, and energy-efficient logistics to meet these expectations.
4. Enhanced Focus on Supply Chain Resilience
The recent global disruptions, like pandemics and trade conflicts, have underscored the importance of resilient supply chains. Businesses are likely to prioritize flexibility and diversification in their supply chains to better manage future disruptions.
This could involve diversifying suppliers, increasing inventory buffers, or investing in predictive analytics to quickly respond to supply chain risks.
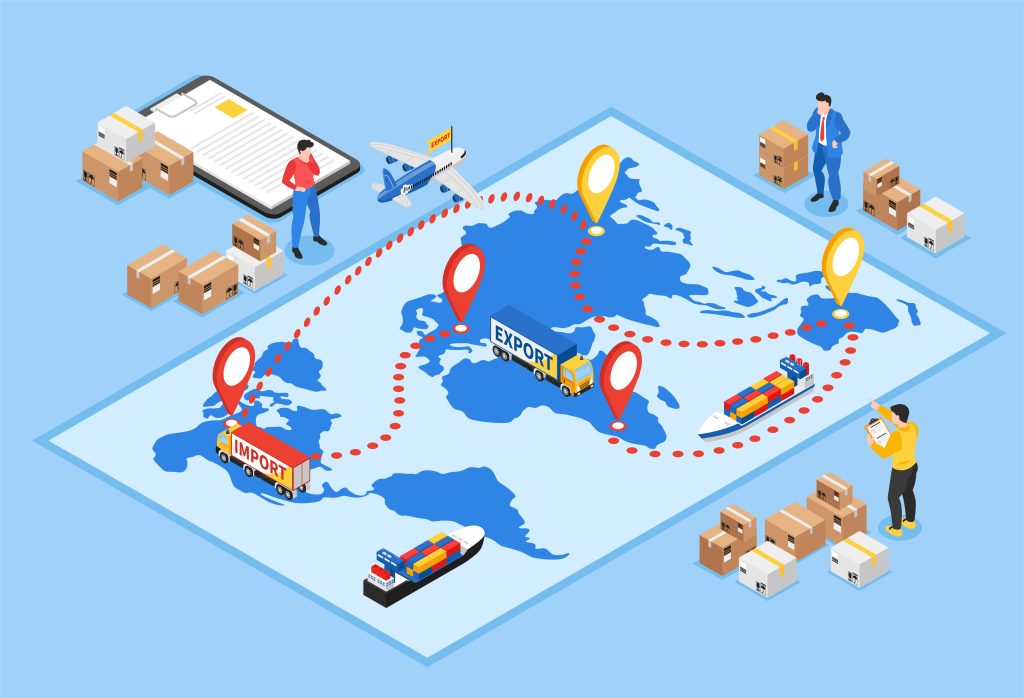
5. Personalization and Customization
As consumer preferences shift towards personalized products, supply chains must adapt to accommodate small-batch production and faster turnaround times.
Advanced manufacturing technologies, such as 3D printing, are enabling companies to offer customized products without significant increases in cost or production time.
6. Advanced Analytics and Big Data
The use of big data and advanced analytics in SCM is set to increase. These tools can provide deep insights into consumer behavior, supply chain performance, and market trends.
Companies can leverage this data to make informed decisions, anticipate market changes, and better align their supply chain strategies with business goals.
7. Supply Chain as a Service (SCaaS)
Cloud-based platforms will enable more businesses to outsource their supply chain management to third parties.
This “Supply Chain as a Service” model can help smaller companies leverage advanced SCM technologies and expertise without significant upfront investments, thereby leveling the playing field between small and large businesses.
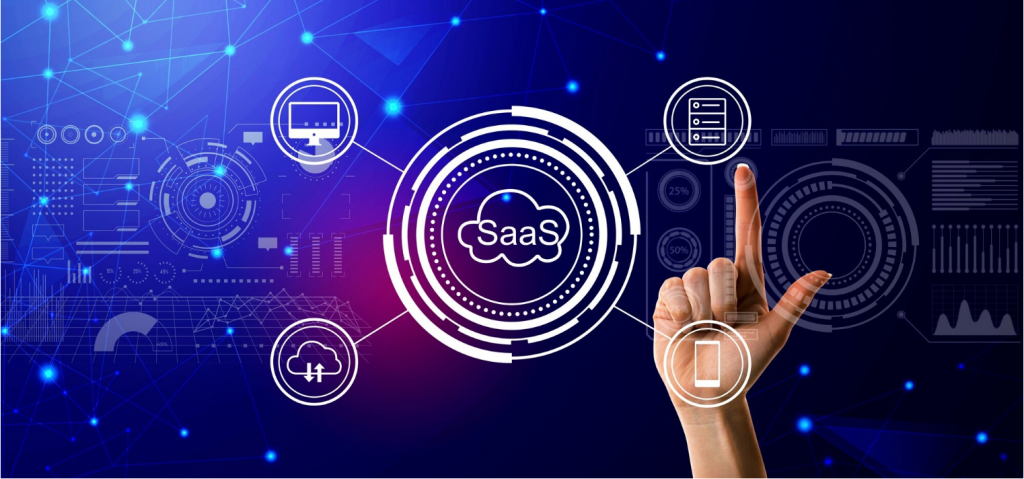
8. Collaborative Ecosystems
There will be a shift towards more collaborative supply chain ecosystems, where businesses, even competitors, share data and resources to optimize supply chain efficiency. This collaboration can lead to improved product lifecycles, reduced costs, and enhanced innovation.
🔥Conclusion
Supply Chain Management is more than just moving goods from point A to point B. It’s about strategically optimizing processes to ensure maximum efficiency, cost-effectiveness, and customer satisfaction.
As businesses continue to navigate the complexities of global markets, effective SCM becomes crucial for maintaining competitive edges and ensuring long-term sustainability.

Understanding and implementing effective supply chain management practices can lead businesses not only to operational excellence but also to notable growth and development.
Whether you’re a seasoned business owner or a budding entrepreneur, investing time to understand and optimize your supply chain can yield significant dividends.